

Defect performance (or the Quality in OEE).

Some maps are more comprehensive but not always necessary. The following information is needed to construct a value stream map (at a minimum). Of course, the company goals should have Customer Satisfaction as priority. The future state should be aligned with company goals, mission, and vision. The team should get creative and develop the future state regardless of what they think can be accomplished with some discretion as to what is practical and economical. The key here is to make a meaningful change, get a quick win and something accomplished that people believe (and can verify financially) made a positive difference.ĭevelop the desired future state and long-term vision. Select a specific product family, set of machines, group of people if it isn't possible to implement improvements across everything. This helps with the next iteration of improvements. The objective is to begin to change the paradigm or the culture and make the positive change visible. so these numbers can be used as baselines to compare against actual observations.ĭevelop a short term (with the week or a few weeks) map that is achievable with existing resources. It is ideal to get a long run historical sampling of data for Changeover Times, Machine rates, Quality, etc. Be consistent with how the values are obtained and used on the map. It is important to prepare for this as a GB/BB when leading the team so a consensus can be reached on all the "what-if" scenarios. There are often situations where cycle times vary, batch sizes vary for appropriate reasons, and it is difficult to come up with values for the map. There may be a short term and longer term future state map depending on the how detailed the team wants to proceed.Ĭapture the current process despite how ugly it may be. and possibly a FUTURE STATE (LONGER TERM).Two maps, at a minimum, are needed to represent the: When value stream mapping, it is necessary for two maps created (possibly more). It can be done on a computer or on paper with a pencil. reduce lead time and "bad" inventory (free up cash!).create Kaizen projects or Six Sigma projects to achieve future state.identify constraints (also use Takt Time and Line Balancing tools).identify value-added and non-value added waste with quantification.
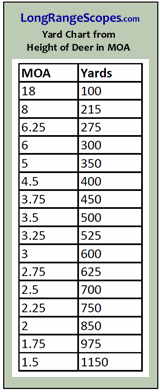
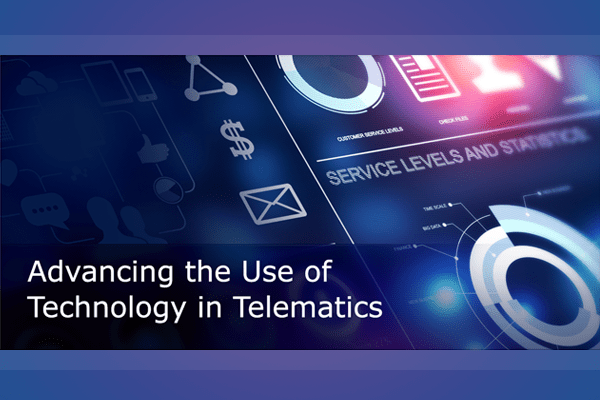
This also could mean traveling to observe processes that occur outside of your location. However it also involves a Gemba walk to observe the actual process and document actual cycle times, actual inventory levels, quality, etc. Value Stream Mapping is more detailed than a Process Map since it is supported with numerical analysis. This will get the team members motivated. After all the hard work of creating the map and agreeing to numbers, the value-added percentage is usually shocking.and it means OPPORTUNITY. Īctually, many processes have < 1% of value-added time. Most current state value stream maps find that <5% of the total lead time for a process is value-added ("value-added" means the time is spent adding value to the product or service which the customer is willing to pay for it or it is compliance/regulatory time).
